text.skipToContent
text.skipToNavigation
La fundición del aluminio requiere romper una gruesa costra de criolita muchísimas veces seguidas a altas temperaturas. Por eso, a Damco Aluminium Delfzijl Coöperatie (Aldel) no le bastaba con utilizar un cilindro normal. Esto contrasta con el nuevo rompe-costra. Diseñado por IMI Norgren y suministrado por itsme, este cilindro durará años y servirá para romper la costra muchísimas veces.
Unos ochenta hornos. Había más que no se utilizaban cuando André van der Ploeg empezó a trabajar para Damco Aluminium Delfzijl Coöperatie (o Aldel). La empresa acababa de recuperarse de una quiebra y los procesos se iban poniendo en marcha de nuevo con cuidado. Y ahora, que no han pasado ni dos años, hay en funcionamiento 230 hornos de un total de 304. Repartidos por dos enormes naves, garantizan la producción de aluminio líquido que, una vez solidificado, abastece a fábricas nacionales y extranjeras.
Sería raro que André y sus colegas no pudieran utilizar los 304 hornos dentro de poco tiempo. “Nuestra empresa ha crecido mucho y sigue haciéndolo. Cuando empecé aquí, teníamos una plantilla fija de 170 empleados. Ahora, afortunadamente, tenemos el doble” afirma André.
Aquí en Farnsum, en el municipio de Delfzijl, al noreste de Groningen, una empresa como Aldel es un importante creador de empleo a nivel regional. El propio André trabaja para el fabricante de aluminio como un gestor de activos y se encarga de la integridad, la disponibilidad y el mantenimiento (preventivo y correctivo) de las instalaciones en las dos naves gigantes.
Trabajo emocionante, así lo llama. “Lo que hay que hacer en estas naves es abastecer de aluminio líquido a nuestra fundición. Y eso es un proceso continuo que implica mucho trabajo”.
Añadir la alúmina aleatoriamente no tiene sentido, dice André. Hay que empujar la materia prima para que atraviese la costra de criolita. De esto se ocupan dos cilindros en cada horno, los cuales rompen la costra incontables veces.
“Cada 24 horas añadimos dos toneladas de alúmina al contenido de un horno. Lo hacemos en dosis de dos kilos cada vez, lo que significa que cada cilindro rompe la costra más de veinte veces cada hora”.
Los cilindros que hay instalados en los hornos de Aldel funcionan, pero son muy viejos. Al empezar de nuevo, se detectó que era necesario un mantenimiento muy urgente, pero la revisión supuso un gran reto para la capacidad de resolución de problemas que tienen André y sus colegas.
“Nuestros cilindros ya no se fabrican. Por suerte, todavía tenemos existencias de reserva y también podemos utilizar las piezas de los cilindros de los hornos que siguen fuera de servicio. Pero eso solo es una solución temporal. Sobre todo ahora que vamos a utilizar todavía más hornos”. Así que André se fue a buscar un cilindro nuevo. Lo más evidente habría sido, quizá, ponerse directamente en contacto con un fabricante, pero a André no le convencía esa estrategia. “Porque ¿cómo podía saber yo que así obtendríamos la mejor solución? Me decidí por la certidumbre. Así que me puse en contacto deliberadamente con itsme, con quien llevamos trabajando muchos años. itsme nos ofrece su apoyo en aspectos mecánicos y de ingeniería eléctrica, es rápido y no se compromete con ninguna marca. Y esto último es lo que yo consideraba más relevante para lo que buscábamos”.
Así, André recibió el año pasado varias ofertas enviadas por Herbert Sturing, comercial de servicio de producto de neumáticos en itsme. Tras un exhaustivo proceso de selección, explica Herbert. “No nos limitamos a escoger varias marcas al azar, sino que hicimos una selección muy consciente basándonos en las necesidades de Aldel. En itsme, sabemos mucho sobre neumáticos y tenemos los conocimientos para esbozar un panorama completo de las posibilidades. Eso es lo que asegura una conexión óptima entre el cliente y el fabricante”.
De las tres sugerencias, la mejor acabó siendo la de IMI Norgren. En parte por su detallado diseño, pero, según André, también por la experiencia de IMI Norgren con este tipo de cilindro. “La compañía no deja nada al azar, y con esto ha sido igual. Al igual que Herbert, también Erik de Jager, de Norgren, vino por aquí periódicamente y juntos encontramos la solución adecuada. Todos los implicados dedicaron mucho tiempo y energía a este proyecto. Y lograron su objetivo”.
Por ahora, tan solo se trata de una copia del cilindro de Norgren. Con un peso de casi ochenta kilos, un pistón de veinte centímetros de diámetro y un recorrido de setenta centímetros, desde el final del verano de 2019 el rompe-costra hace su trabajo a pleno rendimiento, y André está muy satisfecho. “El cilindro trabaja sin fallos. Para nosotros este el punto de partida. Ahora ya sabemos qué cilindro tenemos que comprar. Porque tenemos claro que vendrán más”.
ATRAVESAR LA CRIOLITA CON VIGOR
El rompe-costra de IMI Norgren supera la prueba en Aldel
La fundición del aluminio requiere romper una gruesa costra de criolita muchísimas veces seguidas a altas temperaturas. Por eso, a Damco Aluminium Delfzijl Coöperatie (Aldel) no le bastaba con utilizar un cilindro normal. Esto contrasta con el nuevo rompe-costra. Diseñado por IMI Norgren y suministrado por itsme, este cilindro durará años y servirá para romper la costra muchísimas veces.Unos ochenta hornos. Había más que no se utilizaban cuando André van der Ploeg empezó a trabajar para Damco Aluminium Delfzijl Coöperatie (o Aldel). La empresa acababa de recuperarse de una quiebra y los procesos se iban poniendo en marcha de nuevo con cuidado. Y ahora, que no han pasado ni dos años, hay en funcionamiento 230 hornos de un total de 304. Repartidos por dos enormes naves, garantizan la producción de aluminio líquido que, una vez solidificado, abastece a fábricas nacionales y extranjeras.
Sería raro que André y sus colegas no pudieran utilizar los 304 hornos dentro de poco tiempo. “Nuestra empresa ha crecido mucho y sigue haciéndolo. Cuando empecé aquí, teníamos una plantilla fija de 170 empleados. Ahora, afortunadamente, tenemos el doble” afirma André.
Aquí en Farnsum, en el municipio de Delfzijl, al noreste de Groningen, una empresa como Aldel es un importante creador de empleo a nivel regional. El propio André trabaja para el fabricante de aluminio como un gestor de activos y se encarga de la integridad, la disponibilidad y el mantenimiento (preventivo y correctivo) de las instalaciones en las dos naves gigantes.
Trabajo emocionante, así lo llama. “Lo que hay que hacer en estas naves es abastecer de aluminio líquido a nuestra fundición. Y eso es un proceso continuo que implica mucho trabajo”.
950 grados Celsius
La fundición del aluminio se lleva a cabo en unas circunstancias especiales. Hay que considerarlo industria pesada, en la que cada horno contiene una gruesa capa de criolita a una temperatura media de 950 grados Celsius. Al añadir la alúmina se obtiene aluminio puro gracias a un proceso de electrólisis.“Cada 24 horas se ponen dos toneladas de alúmina en un horno”
Añadir la alúmina aleatoriamente no tiene sentido, dice André. Hay que empujar la materia prima para que atraviese la costra de criolita. De esto se ocupan dos cilindros en cada horno, los cuales rompen la costra incontables veces.
“Cada 24 horas añadimos dos toneladas de alúmina al contenido de un horno. Lo hacemos en dosis de dos kilos cada vez, lo que significa que cada cilindro rompe la costra más de veinte veces cada hora”.
Se requería mantenimiento urgente
Los cilindros que hay instalados en los hornos de Aldel funcionan, pero son muy viejos. Al empezar de nuevo, se detectó que era necesario un mantenimiento muy urgente, pero la revisión supuso un gran reto para la capacidad de resolución de problemas que tienen André y sus colegas.“Nuestros cilindros ya no se fabrican. Por suerte, todavía tenemos existencias de reserva y también podemos utilizar las piezas de los cilindros de los hornos que siguen fuera de servicio. Pero eso solo es una solución temporal. Sobre todo ahora que vamos a utilizar todavía más hornos”. Así que André se fue a buscar un cilindro nuevo. Lo más evidente habría sido, quizá, ponerse directamente en contacto con un fabricante, pero a André no le convencía esa estrategia. “Porque ¿cómo podía saber yo que así obtendríamos la mejor solución? Me decidí por la certidumbre. Así que me puse en contacto deliberadamente con itsme, con quien llevamos trabajando muchos años. itsme nos ofrece su apoyo en aspectos mecánicos y de ingeniería eléctrica, es rápido y no se compromete con ninguna marca. Y esto último es lo que yo consideraba más relevante para lo que buscábamos”.
No son solo unas marcas al azar
Así, André recibió el año pasado varias ofertas enviadas por Herbert Sturing, comercial de servicio de producto de neumáticos en itsme. Tras un exhaustivo proceso de selección, explica Herbert. “No nos limitamos a escoger varias marcas al azar, sino que hicimos una selección muy consciente basándonos en las necesidades de Aldel. En itsme, sabemos mucho sobre neumáticos y tenemos los conocimientos para esbozar un panorama completo de las posibilidades. Eso es lo que asegura una conexión óptima entre el cliente y el fabricante”.“Se ha invertido mucho tiempo y energía en ello, y lo hemos conseguido”.

Por ahora, tan solo se trata de una copia del cilindro de Norgren. Con un peso de casi ochenta kilos, un pistón de veinte centímetros de diámetro y un recorrido de setenta centímetros, desde el final del verano de 2019 el rompe-costra hace su trabajo a pleno rendimiento, y André está muy satisfecho. “El cilindro trabaja sin fallos. Para nosotros este el punto de partida. Ahora ya sabemos qué cilindro tenemos que comprar. Porque tenemos claro que vendrán más”.
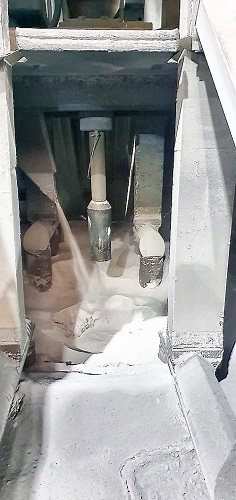
Cuestión de confianzaProcesos pesados, industriales: este es el mundo de IMI Norgren que a finales del año pasado proporcionó a Aldel un robusto rompe-costra. Erick de Jager, ingeniero de ventas de IMI Norgren, rememora con alegría el proceso. “Al final es cuestión de confianza. La confianza en los conocimientos de cada uno, pero también la confianza en que se cumplirán los compromisos. En este proyecto hemos sido una prolongación de itsme en dirección hacia Aldel. Y ha ido bien; el cilindro funciona como tiene que funcionar. Aldel puede avanzar con él, eso seguro”. |
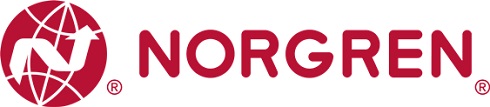
Caer, levantarse y hacerse ecológicosLa historia de Damco Aluminium Delfzijl Coöperatie (Aldel) está llena de acontecimientos. Desde su creación en 1966 la empresa ha pasado por varias quiebras y absorciones. Mientras tanto, ser ecológicos es un aspecto importante para Aldel, por ejemplo, equipando las dos naves de producción con 50 000 metros cuadrados de paneles solares. Menos emisiones de CO2, un mayor consumo de energía sostenible: el futuro de Aldel es tan prometedor como ecológico. |
También te puede interesar esto:
Reingeniería
Leer más
Un reemplazo individual no siempre es algo evidente dentro de los sistemas neumáticos. Los sistemas envejecen, las piezas dejan de producirse. ¿Cómo resolver eso sin tener que detener la producción? Con nuestra reingeniería para la neumática, convertimos un producto descatalogado en una alternativa moderna e integrada. Nuestra gama es amplia; incluye múltiples marcas y, por tanto, ofrece numerosas opciones. También para usted.
Soporte a la ingeniería
Leer más
itsme Industrial Automation conoce su mundo. No solo decimos eso; también lo demostramos. Cuando le visitamos, no adoptamos un enfoque pasivo; itsme Industrial Automation conoce su mundo. No solo decimos eso; también lo demostramos. Cuando le visitamos, no adoptamos un enfoque pasivo. Entramos en acción y nos ponemos directamente manos a la obra para usted. Esa proactividad nos define. Su eficiencia puede verse claramente en nuestros servicios de soporte de ingeniería.