LEUZE DRT 25C The one for everything.
Reliable detection of confectionery and baked goods without readjustment when changing objects.
The DRT 25C dynamic reference diffuse sensor – an innovative new product from Leuze – is specially designed for the detection of confectionery and baked goods. Thanks to intelligent CAT technology it reliably recognizes flat and spherical products, transparent to high-gloss foils as well as irregular shapes and contours.
Sensors must safely detect a wide variety of products and films on the conveyor belts of packaging machines (HFFS, FS, Thermoform, and VFFS) for confectionery and baked goods. In addition, they must work continuously after a product changeover, without requiring further setup. Optical sensors that perform these tasks are typically retro-reflective sensors that operate with foreground suppression. This technology has its weaknesses, however, especially when detecting flat, glossy or transparent objects.
The innovative detection method of the DRT 25C, on the other hand, works with Contrast Adaptive Teach technology, CAT for short, whereby the conveyor belt is used as a reference instead of the product. This is how the reference diffuse sensor detects any type of object as a 'deviation' to the conveyor belt surface. The detection is independent of the surface characteristics of the products, such as the color, gloss, and transparency.
Advantages for you
- The reliable detection of objects even with difficult shapes and surfaces ensures continuous machine output and prevents downtime
- No adjustment of the sensor is needed when products or packaging materials are changed, shorter setup times enable higher production quantities
- Fast and easy setup of the sensor through automatic teaching of the belt surface using the teach button; just one universal mounting position for all objects
- Reliable operation even if the conveyor belt is dirty or vibrating
- IO-Link for easy integration of additional functions in the machine control, such as warning message in case of excessive contamination, use of the counter built into the sensor, or locking of the teach button
How does the DRT 25C work:
For trouble-free control of the buffer section, packaging made of various materials and with a wide variety of surfaces must be reliably detected from the front edge. Changing products or packaging films should not require any additional setup and adjustment work on the sensor.The unique technology of the DRT 25C uses the conveyor belt surface as the point of reference. The detection is independent of the surface characteristics of the materials used, such as the color, gloss, and transparency. This means no setup work on the sensor is required when changing products.
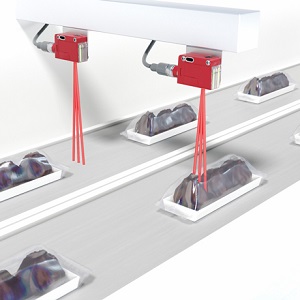
Three light beams for maximum reliability
No matter what shape the confectionery and baked goods and their packaging have: With its three light beams, the DRT 25C reliably detects the front edges of the objects and ensures that the process goes smoothly without any machine downtime. Thanks to the wide scan, even products with holes, such as cookie curls, are safely detected as a continuous object. For this, not all three light spots need to be on the object.
From transparent to high-gloss
Packagings with different colors and transparency are safely detected as a ‘deviation’; from the conveyor belt surface due to the reference technology. This means that even machines that process a wide range of films can be equipped with a single sensor type.
No setup time when changing products
When performing the initial setup, the conveyor belt surface is taught in as a point of reference with the teach button. After a product changeover, it is not necessary to adjust this setting, as the point of reference remains the same. In addition, the mounting position and the alignment of the sensor itself can be continuously used for the widest variety of objects. This means that no setup effort is required for the sensor when changing products.
One-of-a-kind CAT technology
The DRT 25C works with the conveyor belt surface as a dynamic reference for the detection of objects. With this method, the surface characteristics of the conveyor belt are taught in via the teach button. The sensor will then detect all objects that do not correspond to the conveyor belt surface. Even contamination on the conveyor belt can be compensated with the Contrast Adaptive Teach technology.
Technical properties
- Reference technology and three LED light spots for reliable object detection with the widest variety of shapes and surfaces
- Large working range for conveyor belt spacings of 50-200 mm
- High switching frequency of 750 Hz for belt speeds up to 2 m/s
- Easy configuration via an operating button (teach button)
- IO-Link interface for standardized communication with the machine control in the dual channel principle or in SIO mode
- Compact housing: only 15 mm x 42.7 mm x 30 mm for universal use
- Protection classes IP 67 and IP 69K and ECOLAB certification
Detailed product information about the DRT 25C-M you find here
Product video with smart features explained